RPAで成功した事例はたくさんあります。しかし自社に合う製品や、どのように検討したらいいのかわからない。こんな不安があったりします。そこでこの記事では、RPAの解説から主な機能、導入に成功した企業の事例から失敗しないポイントを紹介していきます。
目次
RPAとは何か
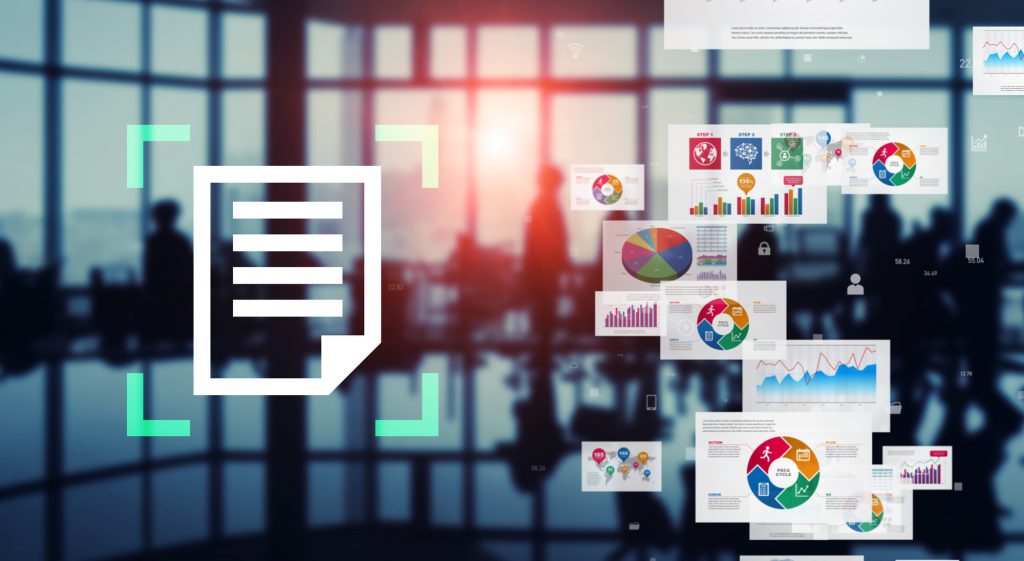
RPAは(ロボティック・プロセス・オートメーション)の略称で、今まで人だけが対応できるとされていた作業が、AIの機械学習等を活用し代行・代替できる仕組みのことを言います。RPAの主な機能を見ていき、導入事例を参考にしながら、自社と照らし合わせていきましょう。
RPAの主な機能
RPAはAIと同じ意味に思われがちですが明確な違いがあります。AIは学習能力があり、自ら判断して決定事項も独自で行います。音声の文字化、画像の認識などは単純作業ではできず、人のような見分け方が必要です。学習が必要な作業にはAIが向いていると言えるでしょう。
一方でRPAは、作業の自動化なので学習能力は備えていません。たとえばデータの分析や収集を自動化することまでできます。RPAは決まった作業以上の効果を期待するより、効率化を図る使い方がされていると言えるでしょう。
RPAの具体的な機能は次のようなものがあります。
レコーディング機能
マウスやキーボードの動作を記録して、パソコン上の一連の作業を自動化できる機能です。レコーディングをスタートした後、自動化したい作業をパソコンで実行すると、作業のすべてが記録されます。
この記録する作業だけで、自動化が実現できます。単純作業を自動化するだけなので、専門家でなくとも自動化の仕組みを作成することができ、効果を実感しやすいです。
自動化する部分は全てでなくとも、部分的に使うことができ人の手を使うべきところの把握にも役立てることが可能と言えます。
スクレイピング機能
スクレイピング機能とは、Webサイト上のデータを取り込む機能です。データを自動的に認識して、高速かつ容量大で取り込むことができます。この機能があれば、情報収集にかける時間を大幅に削減することが可能です。
たとえば競合他社の商品などの情報を取得し、ExcelやCSVに書き出して保存したり、メールで送信したりすると、まとめる時間が短縮できます。操作も簡単で、あらかじめルールを決めておき、ボタンを押したら自動的にデータの取得が行われます。
Web上の大量の情報を取得して集計して活用することは、マーケティングにおいて必須です。このスクレイピング機能をうまく活用することができれば、他社に大きな差をつけることができます。
RPAの導入が注目される理由とは

RPAの導入が注目される理由としては主に3つあります。
- 人材確保が困難
- 規制の強化
- 非効率的な動きを削除
1つ目は人材確保が困難な時代なので、人に代わって作業する代替役が求められているからです。AIが台頭してくる理由と同じように、人手不足の代替は人を多く集めるより、RPAの導入のほうが効率的な動きになります。また、新たに人材を増やせば人件費も高くなる上、効率化を実施するためにも、RPAの導入は注目されると言えます。
2つ目の理由は規制の強化です。情報漏洩の点などでも、人手による管理は漏洩がしやすいのは、これまで漏洩した事例が多く語っているでしょう。いずれは対応しなければならない規制を先読みした導入を見込む企業も増えています。
3つ目は、非効率的な動きを削除することです。人材確保よりRPAを導入検討したほうが費用対効果が見やすいのは事実です。人手不足への対応と、効率化から自社の経営状態を改善していく動きが強まっています。人材確保がしづらい時代で、効率化と経営状態を上げていくには、RPAの導入に注目が集まるのは自然な流れかもしれません。
次の章ではRPAの導入に成功した事例を紹介していきます。
RPAを導入した成功事例を一挙紹介
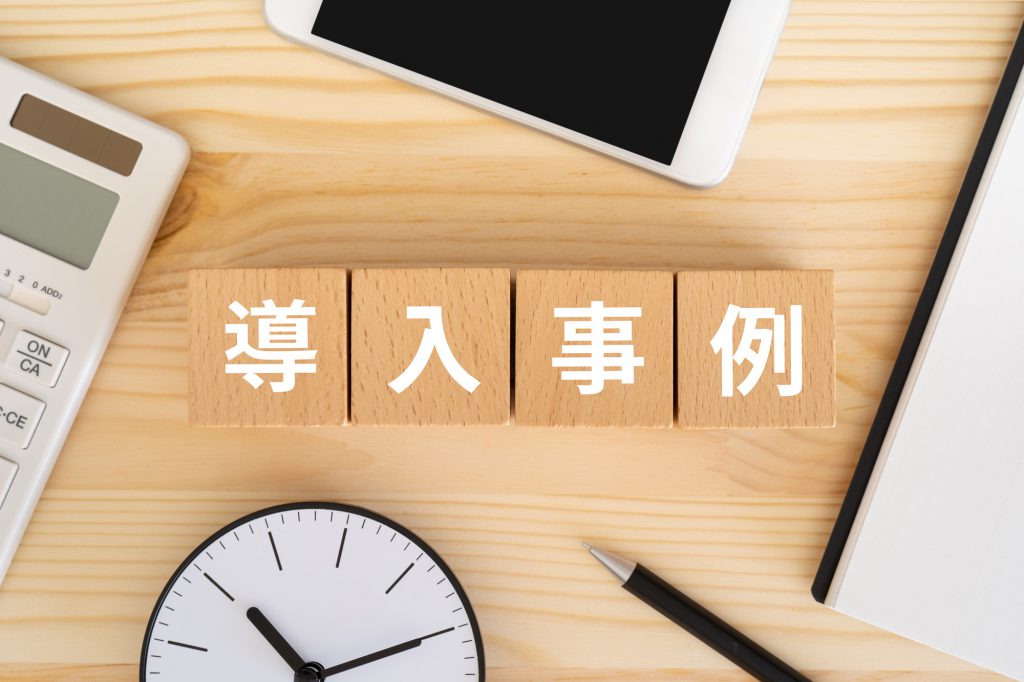
RPAの導入はすでに多くの企業または官公庁で始まっており、主に人手による作業が多い職種で積極的に使われています。たとえば金融機関は顧客データとお金を扱う事が多く、自動化が難しい一面があります。役所などは事務作業が多く、データの漏洩に気を遣う場面も多いです。そんな中でRPAの導入を決定し、新しい活路を見出している企業もあります。今回は一例をまとめました。
楽天カード
楽天カード株式会社は楽天グループの会社で、クレジットカードを扱っています。一切止めることができないのがカードの決済システムで、システムからログ(記録)を抽出して加工や分析が伴う作業が例外的にありました。
サービス維持のためシステムを止めることは難しく、人手による作業が発生し、イレギュラーな対応でも200種類の手作業が発生していました。業務が不定期で、多種に及ぶことが悩みの種で、何とか作業工数の圧縮が出来ないかとRPAの導入に至ったようです。
製品はNTTデータのWinActorで決め手となったのは、自社のパソコンで始めることができ、専用のサーバー構築の必要がなかったことでした。顧客のお金を扱うカード会社なので、導入は慎重にしたと振り返っています。
そんな楽天カードはRPAの導入には注意点が必要と言っています。それは自動化するシナリオを作成する人は、限定したほうが良いということです。プログラムの知識がなくともシナリオを作成できる点はメリットである分、デメリットもあり乱立される可能性も高いです。
導入をきっかけに新たなステージに入りました。RPAで集めたログを未来予測のツールとして利用しているとのことです。業務の自動化から未来の予測と、本質を求める動きがありこれからの活動に期待できます。
三井住友銀行
1,400台以上のソフトウェアロボットを稼働させながらも、年間100万時間以上のパソコン作業を削減することに成功したのが、三井住友銀行を中心とする三井住友フィナンシャルグループです。
三井住友FGは2017年1月からRPA活用の準備を始めました。同年4月に本格稼働が開始され、銀行内にRPAの導入を支援する組織を設けて普及の迅速化を図ります。また。大手コンサルティングファームからITコンサルタントなど約150人を派遣してもらい、行員向けにRPAの研修を行うなどして導入を進めてきました。
例えば営業店への導入事例では、顧客向け運用リポートの作成にRPAを活用。従来は毎朝出社後に、その日訪問する顧客向けのリポートを手作業で作成していました。この作業を代替し、その日に訪問予定の顧客の情報を洗い出し、顧客の最新情報を収集して自動でリポートを作成するようにしていきました。すると営業担当者はリポートをチェックするだけで済み、作業時間を8割削減することに成功したと言います。
神奈川県庁
行政も積極的にRPAを活用する動きがあります。こちらは実験段階ですが神奈川県庁の事例です。
2018年9月から神奈川県庁において、RPAを活用した業務の自動化の有効性を検証する実証を行いました。実証期間は約3カ月間。効果を検証する業務は2つありました。1つは「職員の通勤手当の認定業務」の検証。約2,000件の通勤手当の認定業務をRPAによって自動化すること。
もう1つは「災害時の職員の配備計画作成業務」。毎年作成している勤務時間外と休日に災害が発生した場合の配備人員名簿の作成業務を、RPAによって自動化すること。
実験においても大半の業務は自動化ができたと振り返っていました。休日といった人手ではできない時間帯でも活用できることに効果があると印象が強かったようで、業務を見直すきっかけとして考えていく方向です。
沖縄県那覇市のおもと会グループ
おもと会グループは沖縄県那覇市にある医療、社会福祉、学校法人を擁するグループです。サービス向上のため、DX化や教育制度の充実を惜しまず、RPAの導入も積極的に行いました。RPAの導入は人手作業が多い業界にDX化を推進する役割があり、同グループは時代を先読みした動きを見せています。
コンピューター上の定型業務を自動化するロボット・RPA導入プロジェクトを実施。その結果は、1ヵ月の総労働時間のうち、130時間の削減につながったと言われています。また、法人の種類が異なるため、連携において課題が多いと課題意識を持っており、ソーシャルな課題を解決するグループを目指していると同グループの理事長が話しています。
葛飾区
東京都葛飾区は、外部スタッフに報酬を支払う際の源泉徴収の精算処理業務にRPAソフトを導入しました。2017年にテストで検証し、年間444人日の作業工数を削減した実績を元に導入を決定。職員の労働時間を削減できたほか、事務ミスが減ったことで事務の品質が向上したと言います。
これらの事例から言えるのは、RPAは人手作業の効率化に適していることです。アイデアを生み出すには、過程をクリアにしていくことから生まれてきます。各事例からも、アイデア作りのきっかけとしてRPAの導入が進んでいると言えるでしょう。
次の章では失敗しないRPAの導入ポイントを解説していきます。
RPA導入に失敗しない3つのポイント
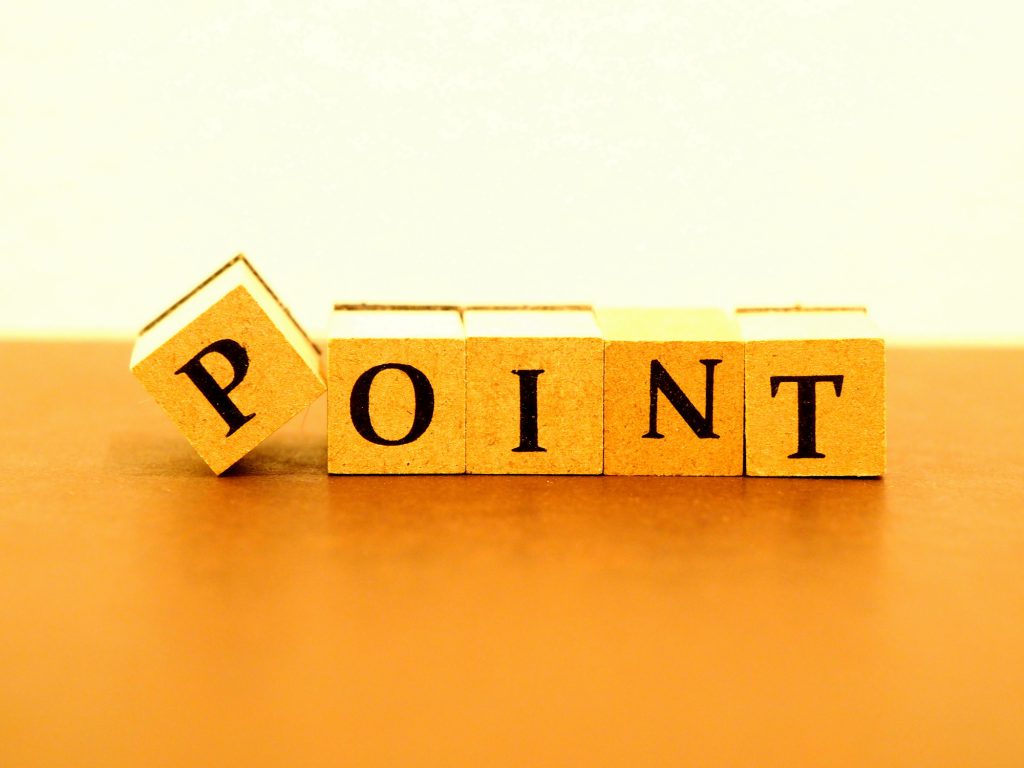
RPAはこれまでの事例紹介から、手作業の削減に大きな貢献ができるものというのがわかりました。しかしながら、メリットだけで導入を決定すれば自社の業務で何を改善できて、どのような効果が見込めるのか?これらが把握しづらいです。そこでこの章では、RPAの導入に失敗しない3つのポイントを解説していきます。
RPA導入の目的を明確にする
1つ目のポイントはRPA導入の目的を明確にすることです。どれくらいの費用対効果、効率化ができるのかは、導入してみないとわからない点があります。RPAは自動化に優れており、新しいアイデアを出すAIのような提案には不向きと言えるでしょう。導入効果に過剰な期待を込めると、投資失敗になる可能性が高いです。ですので導入目的はある程度明確にしておくことが重要です。目的を定めるには、次のようなステップを踏むと納得を得やすいです。
- RPA製品の特徴を知る
- 自社が解決したい課題を洗い出す
- RPAで解決できる箇所を定める
- 削減できる時間や作業を見込む
機能がどう自社に良い働きをもたらすのかまでシュミレーションすることは、導入前でもできます。目的に沿った導入を勧めていくことで、RPAの導入は成功したと言える状況になってくるでしょう。
運用のルールを決めておくこと
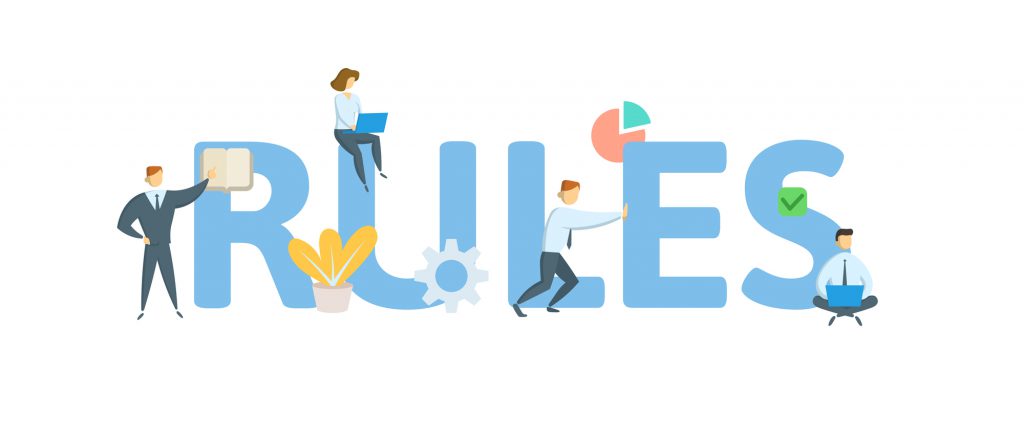
2つ目のポイントは、運用のルールを決めておくことです。楽天カードの事例にもあったとおり、運用できる人数を決めておくことで、セキュリティ対策と人の役割が明確になりやすいです。また、管理面でも効率化となり、ルールはあらかじめ決めておくことがベストと言えます。次のあたりを決めておくことで、運用ルールが明確になってきます。
- RPA導入の管理者と運用者の人数
- トラブル時のマニュアル
- RPAを適用する業務の範囲
また、導入後はRPAの稼働する業務範囲を絞ることで、スタート時の混乱を避けることができます。一度に自動化するのは反対に手数が増えることも予想できるため、運用の日数も効果を見ながら実施することで、RPA導入をスムーズにするコツになるでしょう。
RPAの得意なことを把握する
3つ目のポイントはRPAの得意なことを把握することです。先述の通り人手の作業を自動化することが主な機能です。ですので、複雑な業務内容をRPAに依存しないことが重要になってきます。RPAの機能を理解しておけば、自社が必要とする箇所の特定から、行動するべき内容までが見えてきます。
これら3つのことは基本的なことで、導入後も効果に影響しやすい事柄と言えるでしょう。導入範囲を明確にすること、RPAの運用可能な箇所を把握することで成功事例となっていき、業務をスマート化からDX化へと繋がっていく流れが作れます。次の章では、代表的なRPA製品を紹介していきます。
RPAのお手軽なツール3選
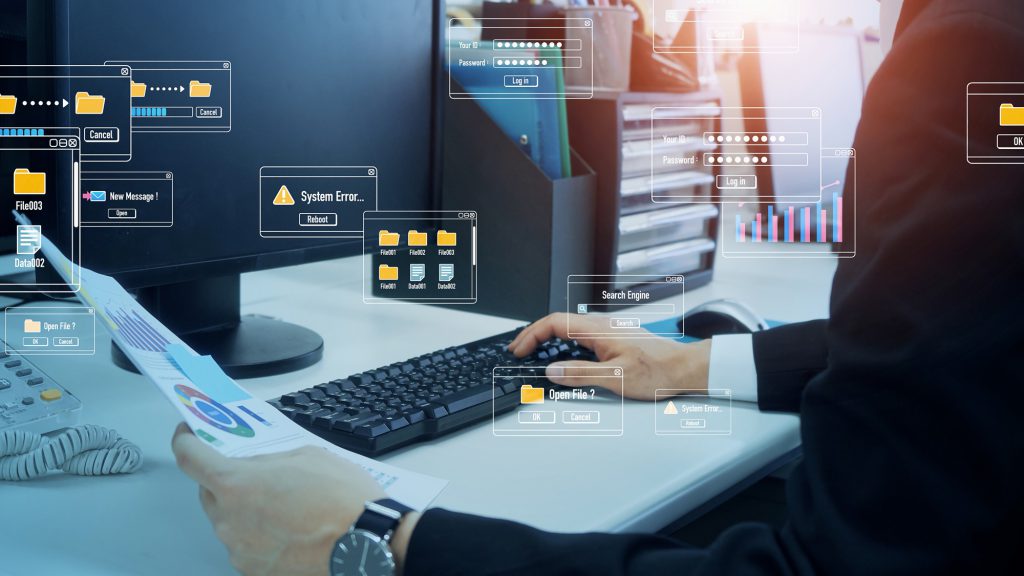
RPA製品の導入が決まっても、製品化されたものは多くあります。そこで初めてでも導入しやすいお手軽なツールを3つ紹介します。簡単に利用でき、運用のルールも簡略化されており、初回の投資としては扱いやすいと言えるでしょう。
WinActor(NTTアドバンステクノロジ株式会社)
WinActorはNTTが提供するRPA製品です。楽天カードが導入した製品でもあり、長い歴史と豊富な実績から信用を得ています。
特徴としては、利用できるアプリケーションに制限はなく、あらゆる業務を自動化できる仕様です。自動化のロボット作成も容易で、プログラミングの知識は不要、情報システム部のようなIT部門でないユーザでも簡単に自動化が可能です。
そのため、業務改善のタイミングやシチュエーションは問わず、ロボットに定型処理を任せることで、本来の業務や新規ビジネスに専念することができます。また、無料トライアルの期間があるので、お試し利用をして効果を検証することができます。
RoboTANGO(スターティアレイズ株式会社)
RoboTANGOは、デスクワークにおける単純作業を自動化するRPAです。プロダクト名の由来は「It takes two to tango.」 ビジネス会話にも使える世界的に有名なことわざで 「それは一人でできるものじゃない」などの意味で使われます。口コミの数とそこからの満足度が高く、サポート体制もしっかりと築いています。月額料金は5万円からですが、こちらも無料トライアルがあります。
EzRobot(株式会社RPAソリューションズ)
EzRobotは劇的にカンタンをモットーにしているRPA製品です。実際の業務と照らし合わせながら一緒にロボット作成ができます。RPAに対する知識がなくても、使った当初から効果を実感しやすいのも特徴です。
パソコン上で動作するものであれば、ほぼ全てのアプリケーションソフトやブラウザ操作が可能です。また純国産の安心感、デスクトップ型なのでセキュリティ面にも優れています。
契約も月毎更新という手軽な導入のしやすさ、パソコンを日常業務で使う方なら感覚的に使いこなせるという点も含め、中小企業にとって非常に扱いやすいツールです。導入費用、サポート料金も完全無料で、トライアル期間もあります。
その他、RPAの製品は多くあります。今回は3つの紹介でしたが各社の機能を見て、自社の課題解決と組み合わさるものを選んでいきましょう。
RPAは日本だけで流行している?海外の事情を解説します
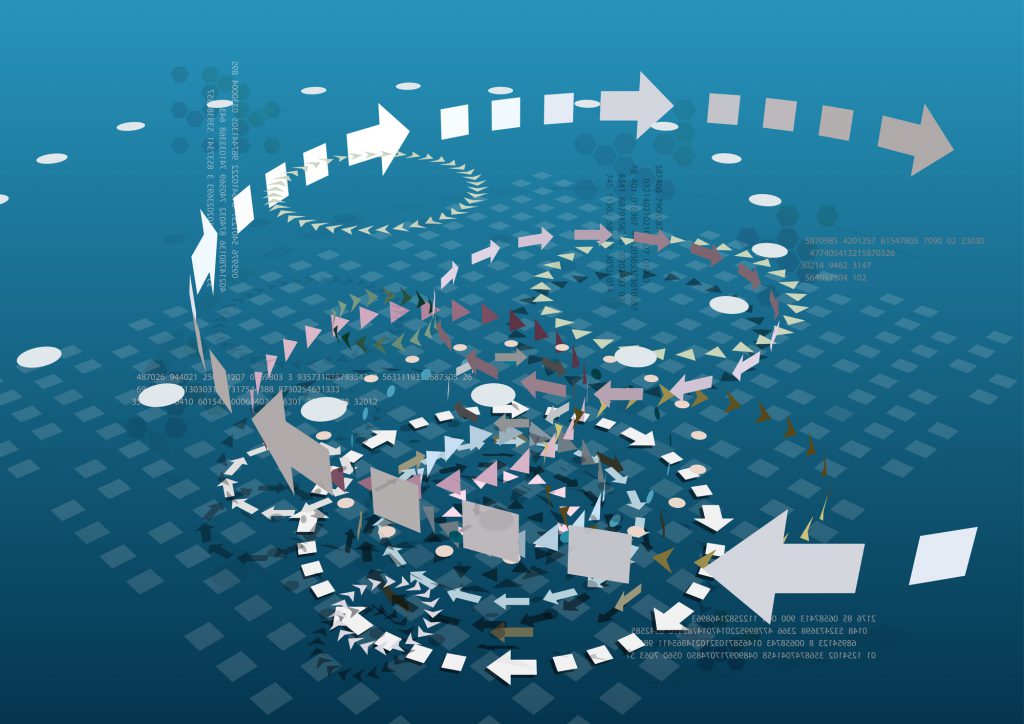
ここまでRPAの解説から導入事例、失敗しないポイントを紹介してきました。RPAは日本だけで流行しているのか?という疑問の声について、海外での状況を解説していきます。
RPAは日本だけではない
RPAの始まりは海外であり、Microsoft社もRPAソフトウェアを展開していることから、RPAは日本だけではないと言えるでしょう。また、RPAを世界規模で見たとき、日本市場のシェア率は25%とされています。
人口分布や一般的なグローバル製品のシェア率から考えると、日本がひときわ高いシェアを誇っていることが分かります。ということは、日本が世界の4分の1のシェアを持っていることになります。
RPAが日本だけと言われる理由とは
RPAが日本だけと言われる理由は、国際競争力の低さが原因とされています。
権威ある世界的ビジネススクールIMD(国際経営開発研究所)の毎年のレポートによれば、最新の2022年版では全64か国中34位でした。この順位からも、日本はデジタル後進国と言わざるをえない状況です。そのため、人手業務が多いことを物語っています。また同時にRPAのような自動化に長けた製品が採用されやすい市場でもあると言えます。
まとめ
この記事ではRPA製品の説明から導入事例、日本のRPA市場の世界から比べた状況をお伝えしてきました。人手の作業が多くデジタル部門では後進国の位置づけな日本では、RPA製品の導入はさらに普及していくでしょう。製品の特徴、自社の改善点等を汲み取りながら最善な行動を試していくことで、変革が生まれていきます。

AI GIJIROKU ブログ編集部です。議事録や、会議、音声を中心に生産性を向上するためのブログを執筆しています。